Quality Month in 2022 - Implementing the Zero Defect Quality Concept of “Doing Things Right the First Time”
To enhance the overall quality awareness and on-site production quality control capabilities, promote the zero-defect quality concept of “Doing Things Right the First Time”, and actively create a quality improvement atmosphere with broad participation, Twowing Technologies has designated November as the “Quality Month in 2022”, during which a wealth of quality activities were carried out.
The theme of this quality month is “Quality=Zero Defects”. Through a series of quality-themed activities, we aim to create an environment of whole-staff action, learning, and participation in quality activities, to enhance the quality awareness of all employees, and to improve the quality of products leaving the factory. The organizer of the activity and the manager of the quality department, Hu Guangjun, called on everyone to start from themselves, start from scratch, and pursue zero defects. During the product manufacturing process, it is crucial to strictly follow the “three complying, two following” principle, which means “operate according to the process, documents, and operation manual, comply with the process discipline, and the labor discipline”. By engaging all personnel at every stage of the entire production process involved in product manufacturing, we aim to comprehensively enhance everyone's quality consciousness.
In this quality activity, we have benchmarked the specific requirements of leading customers in the industry and conducted risk assessments on the product development and manufacturing process. The inspection objects include all relevant links such as R&D, material control, storage, SMT, DIP, assembly testing, quality control, engineering, equipment, and after-sales service. We identified 165 risk issues and 37 improvement items required by customers, with 126 improvement items aimed at achieving the desired state. We actively promoted the development and implementation of improvement measures, confirmed the effectiveness of the measures, and achieved a closed-loop rate of 98.78%.
The implementation of the Quality Month takes zero defects as a challenging goal and adheres to the following principles for quality activity:
Customer-oriented approach;
Full participation in quality training and case studies by all employees;
Judgment and optimization based on on-site inspections and objective facts;
Establishment of reasonable production rates based on different product and customer requirements;
IT-based and visualized quality monitoring;
Adherence to a quality culture that values “Mission Possible”.
Our top priority during this quality activity is to effectively establish a zero-defect quality concept, which emphasizes "Doing Things Right the First Time". We are well aware that any defects or quality issues in our products could lead to heavy costs for both us and our customers. We clearly demand that we must maintain our commitment to the principle of "Doing Things Right the First Time".
During this quality month activity, a total of 96 quality reviews, awareness training, and tool learning sessions were organized by various teams, with a participation rate of 98% for front-line employees and 100% for off-line IDL. After the training and learning, everyone shared the following “words of wisdom”.
Quality is in my heart;
Details determine success or failure;
Talking about quality is fake, confirming it through action is real;
Quality consciousness is built on a correct understanding of quality, and the depth of this understanding reflects the level of quality consciousness.
We held 16 quality competitions themed "Continuous Improvement and Quality First", including "Quality Fault Finding", "Quality Skills Competition", and "Quality Knowledge Quiz". These competitions produced a total of 16 first-place winners, 32 second-place winners, and 48 third-place winners. The participants actively engaged in the competitions with solid quality theory knowledge and superb operational skills, pushing the competitions to new heights and ultimately achieving the goal of improving the overall quality awareness and practical operational capabilities of all employees.
In addition, we also organized an essay competition titled “I am responsible for product quality" and received a total of 663 essays. After the initial selection, 150 essays were chosen with a rating of good or above (and all rewarded with exquisite souvenirs), and after the final selection, 20 outstanding-level essays were awarded Wi-Fi 6 wireless routers.
When talking about the gains and experiences from this year's Quality Month activity, Hu Guangjun, the organizer and the Quality Manager, said, “Quality is the foundation of everything, and the cornerstone for our enterprise's survival and development. Only with quality assurance can enterprises go further."
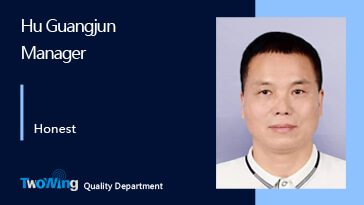